Oznakowanie prawdę Ci powie
„Awaria przemysłowa”, „skutki awarii przemysłowej” – to sformułowania budzące natychmiastowy niepokój opinii publicznej. Nie bez przyczyny. Większość z nas potrafi wymienić co najmniej kilka takich poważnych i niebezpiecznych przypadków. Wśród powodów tych zdarzeń często jest nieprawidłowe oznakowanie niebezpiecznych produktów, któremu jednocześnie bardzo łatwo zapobiec.
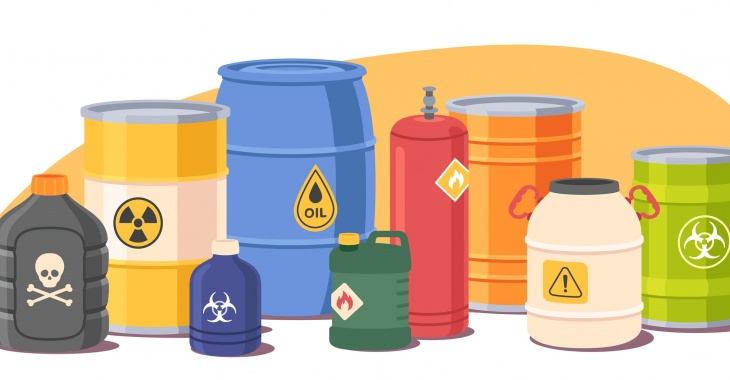
Skutki awarii przemysłowych to wszelkie bezpośrednie lub pośrednie, natychmiastowe lub powstałe po pewnym czasie (opóźnione) następstwa (konsekwencje) dotyczące (między innymi): człowieka, flory i fauny, gleby, wody, powietrza i krajobrazu, wzajemnych więzi między wymienionymi elementami oraz wartości materialnych i dziedzictwa kulturowego [1]. Przykładami przerażającymi w skutkach i możliwymi do znalezienia w ogólnodostępnych źródłach są m.in. wydarzenia w Seveso (1976 r.), w zakładach Bhopal (1984 r, 15 000 ofiar), w Czarnobylu (1986 r.), w Piper Alpha (platforma, 1988 r.), w Fukushimie (2011 r.), w Xiangshui (2019), a także wiele innych. W zależności od rodzaju zakładu, mamy do czynienia ze specyficznymi dla niego procesami fizycznymi i/lub chemicznymi, w związku z czym różne są też zagrożenia, które decydują o tym, jakie ryzyka trzeba wziąć pod uwagę, co będzie zawierał plan awaryjny, itd. Oprócz oczywistych różnic warto zauważyć, że wiele aspektów związanych z bezpieczeństwem w zakładach przemysłowych jest jednak uniwersalnych. Jeden z nich to prawidłowe oznakowanie zbiorników, urządzeń układów rozładunkowych i linii dozujących produkty chemiczne. Temat wydaje się wyjątkowo prosty, po wszechnie znany i uregulowany prawnie. Tym bardziej dziwi fakt, że co roku dochodzi do tak wielu incydentów związanych np. ze zmieszaniem niekompatybilnych substancji w zbiornikach magazynowych. Wiele z nich ma miejsce podczas rutynowych procesów dostawy produktów chemicznych do zakładów przemysłowych.
Nauka na błędach innych
Dostawa i rozładunek produktów chemicznych mogą wydawać się proste w porównaniu do innych procesów odbywających się w zakładzie, ale ponie waż czynności te wykonywane są na dużych ilościach produktów, konsekwencje każdego błędu mogą być bardzo poważne. Przykładowo – 21 października 2016 r., podczas rutynowej dostawy produktów do zakładu w Atchison w stanie Kansas w USA, dokonano niezamierzone go zmieszania dwóch niekompatybilnych substancji chemicznych: kwasu siarkowego i podchlorynu sodu. Doszło do reakcji chemikaliów i uwolnienia chmury gazowego chloru, która bardzo szybko objęła nie tylko teren zakładu, ale również okoliczne tereny zamieszkałe. Kilka szkół zostało ewakuowanych, a około 11 ty siącom mieszkańców nakazano pozostanie w domach przez kilka godzin. Ponad 140 osób, w tym pracownicy, członkowie zespołu ratunkowego, kierowca ciężarówki oraz osoby postronne potrzebowało pomocy medycznej. Część była hospitalizowana. Przyczyn powyższego wypadku było kilka (nie wystarczający system informowania o właściwych punktach podłączeń chemikaliów między firmą a kierowcą dostawcy, brak weryfikacji przez operatora pra widłowego podłączenia przed wydaniem zezwolenia na przepompowanie kwasu, błędy i niekonsekwencje w procedurze rozładunku oraz słabe zrozumienie tej procedury przez operatorów). Jednak najbardziej za skakującym było to, że z pięciu różnych połączeń przy stacji rozładunku tylko jedno (!) było oznakowane. Pracownik zakładu podczas postępowania powy padkowego zapewniał, że wskazał kierowcy, które podłączenie jest tym właściwym, po czym oddalił się. Kierowca zeznał natomiast, że nie przypomina sobie, by pracownik tej informacji mu udzielił. Niestety pod łączenia kwasu siarkowego oraz podchlorynu sodu były bardzo blisko siebie, wyglądały podobnie i nie zostały odpowiednio oznakowane. Kierowca rozpoczął transport kwasu siarkowego do (jak mu się wydawało) właściwego zbiornika i wrócił do kabiny ciężarówki. Dopiero, gdy w bocznym lusterku zauważył rozprzestrzeniający się zielono-żółty gaz, zorientował się, że doszło do pomyłki. W tym czasie 15000 litrów kwasu siarkowego zostało wpompowanych do 22000 litrów podchlorynu sodu.
PRZYKŁADOWE ZDARZENIA, SKUTKUJĄCE UWOLNIENIEM CHMURY GAZOWEGO CHLORU:
|
Wypadki z wytworzeniem toksycznego produktu są oczywiście dużo rzadsze niż te „szczęśliwe”, kiedy produkty nie były niekompatybilne. W takich sytu acjach skutkiem są najczęściej przepełnione zbiorniki oraz straty materialne. Informacja nie przedostaje się wówczas do opinii publicznej, ponieważ „nic się nie stało”. Dla zakładu przemysłowego problem oczywiście jest nadal bardzo poważny. Podstawowym wnioskiem płynącym z przytoczo nych zdarzeń jest to, że zakłady muszą przeanalizować swoje wyposażenie oraz procedury związane z rozła dunkiem produktów oraz wprowadzić zabezpieczenia przed podobnymi zdarzeniami. Mowa o transporcie produktu od bramy zakładu aż do zbiornika docelowego.
Czy droga wewnątrzzakładowa jest właściwie ozna kowana?
Czy na stacji rozładunku znajduje się czytelna, jasna procedura?
Kto powinien być obecny podczas procesu rozła dunku?
W jaki sposób eliminujemy ryzyko błędu ludzkiego?
Czy nasze procedury przewidują sytuację, że kie rowca może nie znać języka lokalnego ani języka an gielskiego?
Czy produkty niekompatybilne mają stacje rozła dunku w odpowiedniej odległości od siebie?
Oraz – wracając do kwestii wydawałoby się naj bardziej podstawowej – czy wszystkie podłączenia, pompy, rurociągi, zbiorniki są właściwie, czytelnie, zgodnie z przepisami oznakowane?
Kluczem jest prawidłowe oznakowanie
Od 2020 r. dostępna jest norma ISO 20560, która ma na celu standaryzację identyfikacji ukrytej i często niebezpiecznej zawartości rur w fabrykach i zakładach. Nowa międzynarodowa norma oznakowania rur wykorzystuje globalnie akceptowane piktogramy GHS na widocznym żółtym tle, aby wizualnie sygnalizować niebezpieczeństwo pracownikom, międzynarodowym wykonawcom i służbom ratowniczym. Określa również rozmiar znaczników na podstawie średnicy rury, aby zapewnić widoczność z daleka. System informacji o bezpieczeństwie rurociągów składa się z czterech kluczowych elementów:
1. Kodowanie kolorami w celu identyfikacji rodzaju zawartości rurociągu.
2. Nazwa produktu stanowiącego zawartość rurociągu.
3. Wskaźnik kierunku przepływu.
4. Tam, gdzie ma to zastosowanie: znaki ostrzegaw cze, piktogramy GHS lub jedno i drugie.
Warto zaznaczyć, że prawidłowe oznakowanie instalacji chemicznych jest istotne nie tylko ze względu na zapobieganie awariom przemysłowym, ale również indywidualnym wypadkom przy pracy. W branży przemysłowej odsetek wypadków skut kujących oparzeniem chemicznym oraz uszkodzenia mi oczu jest nadal niepokojąco wysoki. Przyczyny są oczywiście bardzo różne – z tych powtarzających się – to nieodpowiednie oznakowanie rurociągów lub jego brak. Jeśli weźmiemy pod uwagę liczbę podwykonaw ców na terenie większości zakładów przemysłowych, temat komplikuje się jeszcze bardziej. Jako pracodawcy i/lub osoby zajmujące się BHP nie możemy dopuścić do sytuacji, kiedy większość osób wykonujących prace w pobliżu instalacji nie jest świadoma zawartości danego zbiornika lub rury transportującej produkt. Jeśli prześledzić postępowania powypadkowe, znaj dziemy niestety i takie, gdzie pracownik przyznaje, że zignorował kapiące na niego krople, ponieważ przewód nie był w żaden sposób oznakowany, czyli „pewnie zawierał wodę”.
Prosta przyczyna – poważne konsekwencje
Z powyższych przykładów jasno wynika, że zarówno wielkie awarie przemysłowe, jak i indywidualne wy padki przy pracy miewają tę samą przyczynę – nieod powiednie oznakowanie zbiorników, urządzeń układów rozładunkowych i linii dozujących produkty chemiczne. Należy tu bardzo wyraźnie podkreślić, że prawidłowe oznakowanie nie jest dobrą praktyką, ale koniecznym działaniem w kierunku spełnienia jednego z najbardziej podstawowych wymagań prawnych, czyli zapewnienia pracownikom bezpiecznych warunków pracy. Temat, choć pozornie oczywisty, niestety nie jest poważnie traktowany – a stanowczo powinien. W wielu firmach, zwłaszcza tych prezentujących wysoką kulturę bezpieczeństwa, praktykowane są regularne przeglądy miejsca pracy przez wyższe kierownictwo. Przeglądy te są różnie nazywane (np. Safety Walk), ale idea pozostaje ta sama: podkreśle nie zaangażowania kierownictwa wyższego szczebla w tematy związane z BHP oraz spojrzenie na kwestie bezpieczeństwa „świeżym okiem”, tzn. przez osoby na co dzień niezajmujące się tą tematyką. Przy planowaniu kolejnej inspekcji na terenie za kładu lub podczas dyskutowania kolejnego Safety Walk zachęcam do przyjrzenia się omawianemu tematowi i sprawdzenia, jak on wygląda w państwa zakładzie pracy lub fabryce.
Źródła:
1. Informacje ogólne - DEFINICJE (ciop.pl).
2. Mixing Incompatible Materials in Storage Tanks - English | AIChE.
3. Wrong material + Wrong tank = Trouble - Polish | AIChE.
4. ISO 20560-1:2024.
Informacje na temat Koalicji Bezpieczni w Pracy dostępne są w serwisie www.bezpieczniwpracy.pl.
Artykuł opublikowano w czasopiśmie "Kierunek Chemia" 3.2024
Komentarze